resources
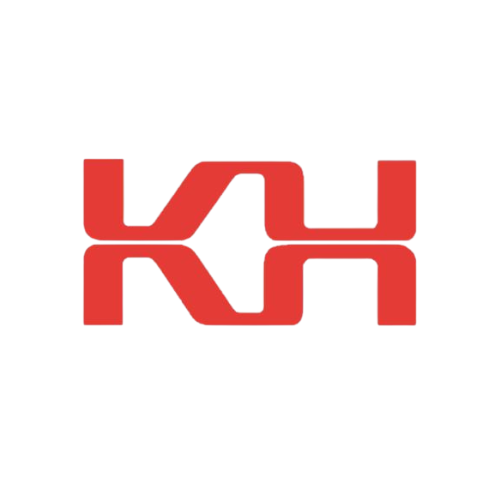
Krohn-Hite Resources
Top 10 Must-Have Electronic Test Equipment for Your Electronics Lab
What Is the Difference Between the RMS Value and the Peak Value?
Choosing the Right DC Calibrator for Your Calibration Needs
What Is the Difference Between an Amplifier and a Preamplifier?
Is a Bandpass Filter Better Than Low-Pass Filter?
What Are the Advantages of a Low-Noise Amplifier?
10 Common Applications of DC Calibrators in Electronics
5 Common Mistakes to Avoid When Using Electrical Test Equipment
AC vs. DC Electrical Power Systems
10 Best Practices for Using Electrical Test Equipment in Hazardous Environments
10 Must-Have Electronic Test Equipment for Your Electronics Lab
10 Must-Have Electronic Test Equipment for Your Electronics LabIn the world of electronics, having the right tools can make all the difference in the success of your projects. Whether you're a hobbyist tinkering in your garage or a professional working in a high-tech lab, having the right electronic test equipment is essential for accurate measurements and troubleshooting.
1. Oscilloscope
An oscilloscope is an essential tool for any electronics lab. It allows you to visualize and analyze the voltage signals in your circuits. With the ability to display waveforms in real time, an oscilloscope can help you troubleshoot problems and measure various electrical parameters accurately. When selecting an oscilloscope, look for one with a high bandwidth and sampling rate to ensure accurate measurements.
2. Multimeter
A multimeter is a versatile tool that can measure voltage, current, resistance, and continuity in circuits. It's an essential piece of equipment for checking the health of components, testing circuits, and troubleshooting problems. Look for a multimeter with a wide range of functions, including auto-ranging and true RMS measurements for accurate readings.
3. Function Generator
A function generator is handy for generating various waveforms, such as sine, square, and triangle waves. It's essential for testing circuits, calibrating equipment, and simulating signals. Look for a function generator with a wide frequency range, low distortion, and adjustable amplitude for versatile use in your lab.
4. Power Supply
A reliable power supply is crucial for providing the right voltage and current to your circuits. Look for a programmable power supply with adjustable voltage and current limits, multiple output channels, and low noise for accurate and stable power delivery. Having multiple power supplies with different voltage ranges can be beneficial for powering various components in your projects.
5. Spectrum Analyzer
A spectrum analyzer is a powerful tool for analyzing the frequency spectrum of signals in your circuits. It can help you identify unwanted signals, measure signal strength, and troubleshoot interference issues. Look for a spectrum analyzer with a wide frequency range, high resolution, and advanced features like peak detection and tracking generators for detailed analysis.
6. Logic Analyzer
A logic analyzer is a specialized tool for capturing and analyzing digital signals in your circuits. It can help you debug complex digital systems, analyze communication protocols, and troubleshoot timing issues. Look for a logic analyzer with a high number of channels, a fast sampling rate, and advanced triggering capabilities for precise signal capture.
7. Signal Generator
A signal generator is a versatile tool for generating precise signals for testing circuits, calibrating equipment, and simulating real-world scenarios. Look for a signal generator with a wide frequency range, low distortion, and adjustable amplitude and modulation capabilities for accurate signal generation in your lab.
8. LCR Meter
An LCR meter is a specialized tool for measuring inductance, capacitance, and resistance in components and circuits. It's essential for characterizing passive components, testing resonant circuits, and analyzing impedance. Look for an LCR meter with high accuracy, a wide measurement range, and advanced features like automatic component identification for efficient testing.
9. Network Analyzer
A network analyzer is a sophisticated tool for analyzing the frequency response and impedance of circuits, components, and networks. It can help you measure reflection and transmission parameters, characterize filters, and optimize matching circuits. Look for a network analyzer with a wide frequency range, high dynamic range, and advanced calibration capabilities for precise network analysis.
10. Electronic Load
An electronic load is a valuable tool for testing the performance and efficiency of power supplies, batteries, and other electronic devices. It can simulate different load conditions, measure power consumption, and analyze voltage and current responses. Look for an electronic load with a wide voltage and current range, high power dissipation capability, and advanced features like transient response testing for accurate power testing in your lab.
Contact Us Today
Having the right electronic test equipment is essential for accurate measurements, efficient testing, and successful projects in your electronics lab. Whether you're a beginner or an experienced professional, investing in quality equipment can make a significant difference in the outcome of your work. Consider the top 10 must-have electronic test equipment mentioned to enhance your lab capabilities and improve your testing efficiency.
Consider Krohn-Hite if you're looking for reliable Electronic Test and Measurement Instruments. As a manufacturer of DC Voltage and Current Sources/Calibrators, Low-Noise Preamplifiers, Wideband Power Amplifiers, and Tunable and Fixed Frequency Electronic Filters, Krohn-Hite offers a wide range of high-quality products for your lab needs. With a commitment to excellence and customer satisfaction, Krohn-Hite provides top-notch service for all their products. Contact us to explore our product lines and learn more about how we can enhance your electronics lab.
Invest in the right electronic equipment today and elevate your testing capabilities to new heights with Krohn-Hite. Your projects deserve reliable and accurate measurements—choose the best equipment for your lab and achieve outstanding results.
What Is the Difference Between the RMS Value and the Peak Value?
When dealing with electrical signals, it's essential to understand the difference between RMS value and peak value. These two terms are often used interchangeably but represent different aspects of an electrical signal's characteristics.
Understanding RMS Value
RMS stands for Root Mean Square, a statistical measure of the magnitude of a varying quantity. In the context of electrical signals, the RMS value represents the effective value of an AC (alternating current) waveform. It is calculated by taking the square root of the average of the squared values of the signal over a given time period.
The RMS value of a waveform is crucial in determining the power dissipated in a resistive load, as it accurately represents the heating effect of the signal. In practical terms, the RMS value of an AC signal is equivalent to the DC (direct current) value that would produce the same heating effect in a resistive load.
Calculating RMS Value
To calculate the RMS value of a signal, the following formula is used:
\[V_{RMS} = \sqrt{\frac{1}{T} \int_0^T v^2(t) dt}\]
Where:
- \(V_{RMS}\) = RMS value of the signal
- \(T\) = Time period over which the signal is measured
- \(v(t)\) = Instantaneous voltage value of the signal at time \(t\)
By squaring the voltage values, averaging them over the time period, and taking the square root of the result, we get the RMS value of the signal.
Understanding Peak Value
The peak value of an electrical signal refers to the maximum voltage or current amplitude reached by the waveform. Unlike the RMS value, which represents the effective value of the signal, the peak value provides the maximum potential of the signal at any given instant.
In simple terms, the peak value of a signal indicates the maximum voltage or current a system can handle without exceeding its limits. It is crucial in determining the overall capability and performance of electronic devices.
Calculating Peak Value
The peak value of a signal can be calculated by simply finding the highest voltage or current value in the waveform. For a periodic signal, the peak value can be determined by analyzing the maximum amplitude of one waveform cycle.
Mathematically, the peak value of a signal can be expressed as follows:
\[V_{peak} = \max(v(t))\]
Where:
- \(V_{peak}\) = Peak value of the signal
- \(v(t)\) = Instantaneous voltage value of the signal at time \(t\)
By identifying the maximum amplitude of the signal, we can determine the peak value of the waveform.
Key Differences Between RMS Value and Peak Value
While both RMS and peak values are important electrical signal measures, they represent different aspects of the waveform. Here are some key differences between RMS value and peak value:
1. Representation: The RMS value represents the effective value of an AC signal, while the peak value represents the maximum amplitude of the signal.
2. Calculation: RMS value is calculated by averaging the squared values of the signal over a time period, while peak value is simply the maximum value in the waveform.
3. Usage: RMS value is commonly used in calculating power dissipation and heating effects, while peak value is used to determine the maximum potential of a signal.
4. Significance: RMS value is more indicative of the true power delivered by an AC signal, while peak value provides information about the signal's maximum capability.
Importance of RMS vs. Peak Voltage in Electronic Testing
In electronic testing and measurement, understanding the differences between RMS and peak values is vital for accurate analysis and evaluation of electrical signals. Both values play a crucial role in assessing the performance and capabilities of electronic devices and systems.
RMS voltage is particularly important in determining the power consumption and heating effects of an AC signal. By calculating the RMS value of a waveform, technicians and engineers can accurately predict the impact of the signal on resistive loads and ensure proper functioning of the system.
On the other hand, peak voltage is essential in assessing the maximum potential of a signal and determining the peak operating limits of electronic components. By monitoring the peak value of a waveform, testers can identify potential overloads and prevent damage to sensitive equipment.
By considering both RMS and peak voltage values in electronic testing, professionals can optimize the performance and reliability of electronic systems, ensuring safe and efficient operation.
How Krohn-Hite Can Help
For precise and reliable electronic test and measurement instruments, look no further than Krohn-Hite. As a leading manufacturer of Electronic Test and Measurement Instruments, Krohn-Hite offers a wide range of products designed to meet the needs of professionals in various industries. Krohn-Hite's product lines include DC Voltage and Current Source/Calibrators, Low-Noise Preamplifiers, Wideband Power Amplifiers, and Tunable and Fixed Frequency Electronic Filters. These high-quality instruments are built to deliver accurate and consistent results, making them essential tools for electronic testing and measurement applications.
Whether you require precise voltage calibration, efficient power amplification, or precise frequency filtering, Krohn-Hite has the right instrument for the job. With a commitment to quality and performance, Krohn-Hite ensures that professionals can rely on our instruments for accurate and reliable results.
Choosing the Right DC Calibrator for Your Calibration Needs
When it comes to calibration in the electronic industry, accuracy is key. Whether you are calibrating testing equipment, sensors, or any other electronic devices, having the right tools for the job is essential. One such tool that is commonly used in the calibration process is a DC calibrator. DC calibrators are used to source and measure DC voltage and current with high accuracy, making them a crucial tool for ensuring the precision and reliability of electronic devices.
Choosing the right DC calibrator for your calibration needs can be daunting, especially with the many options available in the market today.
Understanding the Basics of DC Calibrators
DC calibrators are devices used to generate precise DC voltage and current signals for calibrating other testing equipment. They are often used in aerospace, automotive, telecommunications, and manufacturing industries, where accuracy is essential for ensuring quality control and compliance with industry standards.
DC calibrators come in various shapes and sizes, ranging from portable handheld devices to benchtop models with advanced features. They typically offer a wide range of voltage and current outputs and high accuracy and stability for reliable calibration results.
Key Factors to Consider When Choosing a DC Calibrator
- Accuracy: One of the most critical factors to consider when choosing a DC calibrator is accuracy. Look for a calibrator that offers high accuracy and stability, as this will ensure precise calibration results. Check the specifications provided by the manufacturer to determine the calibrator's accuracy and resolution.
- Voltage and Current Range: Consider the voltage and current range required for your calibration needs. Choose a DC calibrator that offers a wide range of output voltages and currents to accommodate different testing requirements.
- Output Resolution: Look for a calibrator with high output resolution, as this will allow you to generate precise voltage and current signals for calibration purposes. A calibrator with a higher resolution will provide more accurate results.
- Stability: The stability of a DC calibrator is crucial for maintaining consistent calibration results over time. Choose a calibrator that offers low drift and high stability to ensure reliable performance during calibration procedures.
- Calibration Capabilities: Consider the calibration capabilities of the DC calibrator, such as programmable settings, calibration modes, and calibration automation features. These capabilities can enhance the efficiency and accuracy of the calibration process.
- Portability: Depending on your calibration needs, you may require a portable DC calibrator for on-site calibrations or field testing. Choose a calibrator that is lightweight and easy to transport for added convenience.
- Budget: Determine your budget for purchasing a DC calibrator and look for models that offer the best value for the price. Compare features, specifications, and prices from different manufacturers to find a calibrator that meets your requirements within your budget.
Popular DC Calibrators on the Market
Several reputable manufacturers offer high-quality DC calibrators for various calibration applications.
- Krohn-Hite Model 523 Precision DC Source/Calibrator
- Krohn-Hite Model PCR100 100 Ohm Precision Resistor
- Krohn-Hite Model 526 DC Source/Calibrator
Krohn-Hite: A Trusted Manufacturer of DC Calibrators
Krohn-Hite is a leading electronic test and measurement instrument manufacturer, including DC voltage and current source/calibrators. With a reputation for producing high-quality calibration equipment, Krohn-Hite offers a range of precision DC calibrators that meet the needs of various industries and applications.
Krohn-Hite DC calibrators are known for their accuracy, stability, and reliability, making them an ideal choice for calibration professionals and electronic technicians.
Why Choose Krohn-Hite for Your Calibration Needs?
There are several reasons why Krohn-Hite is a trusted manufacturer of DC calibrators for calibration needs:
- High Accuracy: Krohn-Hite DC calibrators offer high accuracy and precision for reliable calibration results.
- Wide Range of Outputs: Krohn-Hite calibrators provide a wide range of voltage and current outputs to accommodate different testing requirements.
- Stability: Krohn-Hite calibrators are designed for stability and low drift, ensuring consistent calibration results over time.
- Excellent Customer Support: Krohn-Hite provides excellent customer support and service for all its products, ensuring customer satisfaction.
- Calibration Capabilities: Krohn-Hite calibrators come with programmable settings, calibration modes, and automation features for enhanced efficiency.
Invest in a Krohn-Hite DC Calibrator for Your Calibration Needs
As you can see, choosing the right DC calibrator for your calibration needs is crucial for ensuring accuracy and reliability in the calibration process. With Krohn-Hite's reputation for producing high-quality electronic test and measurement instruments, investing in a Krohn-Hite DC calibrator is a smart choice for your calibration needs.
Take the next step towards enhancing the accuracy and precision of your calibration procedures by investing in a Krohn-Hite DC calibrator today. Explore our product lines of electronic test and measurement instruments, including DC voltage and current source/calibrators, low-noise preamplifiers, wideband power amplifiers, and tunable and fixed-frequency electronic filters. With Krohn-Hite, you can trust in the quality and reliability of your calibration equipment for years to come.
Amplifier vs. Preamplifier: What is the Difference?
When it comes to amplifying signals in an industrial setting, whether it's for testing equipment or any other purpose, having the right equipment is crucial. Two types of amplifiers commonly used in industrial applications are industrial amplifiers and industrial preamplifiers. While they may sound similar, they serve different purposes and have distinct differences. In this blog, we will explore the key distinctions between industrial amplifiers and industrial preamplifiers, focusing on piezoelectric transducers as a significant area of application for power amplifiers.
Industrial Amplifiers: Power and Signal Strength
Industrial amplifiers, also known as power amplifiers, are designed to increase the power of an input signal. These amplifiers are used to drive signals with high power requirements, providing increased voltage and current output to drive loads such as motors, transducers, and other power-hungry devices. Industrial amplifiers are used in a wide range of applications, from testing to measurement equipment.
One of the key differences between industrial amplifiers and preamplifiers is the amount of power they can deliver. Industrial amplifiers are built to handle high-power signals and drive loads that require significant power output. These amplifiers can amplify signals with high voltage and current levels, making them essential for industrial applications that demand high power delivery.
Piezoelectric Transducers and Power Amplifiers
Piezoelectric transducers are devices that convert electrical energy into mechanical energy and vice versa. These transducers are commonly used in industrial applications for a variety of purposes, such as sensing, actuation, and vibration control. Power amplifiers are often used to drive piezoelectric transducers, providing the necessary power to produce the desired mechanical output.
In industrial applications, piezoelectric transducers require high-power amplifiers to drive them effectively. Power amplifiers designed specifically for piezoelectric transducers are equipped with features such as high-voltage output, high current capability, and low output impedance to deliver the necessary power to drive these devices. These power amplifiers are critical for applications requiring precise control and high output power, such as vibration testing, ultrasound imaging, and precision machining.
Industrial Preamplifiers: Signal Conditioning and Noise Reduction
On the other hand, industrial preamplifiers are designed to amplify weak signals at the input stage before power amplifiers further amplify them. Preamplifiers are used to boost low-level signals with high input impedance and low output impedance, improving signal-to-noise ratio and reducing signal distortion. Preamplifiers are commonly used in applications where the input signal is weak and needs to be amplified before being processed by other equipment.
Preamplifiers are essential for applications where signal fidelity is critical, such as in research and development, testing, and measurement. By amplifying weak signals at the input stage, preamplifiers help improve the system's overall performance, enhancing signal quality and reducing noise and interference. Preamplifiers are also used in conjunction with power amplifiers to provide signal conditioning and noise reduction before amplifying signals to higher power levels.
Key Differences: Power vs. Signal Amplification
The key difference between industrial amplifiers and preamplifiers lies in their primary function: power amplifiers are designed to increase signal power levels to drive high-power loads, while preamplifiers are used to amplify weak signals at the input stage for further processing. Industrial amplifiers are used to deliver high-power signals for driving loads such as piezoelectric transducers, motors, and actuators, while preamplifiers are used to improve signal quality and reduce noise in low-level signals.
Choosing the Right Amplifier for Your Application
When selecting an amplifier for your industrial application, it is essential to consider the specific requirements of your system. If your system requires high power output to drive loads with high power requirements, an industrial power amplifier may be the best choice. On the other hand, if signal fidelity and noise reduction are critical for your application, an industrial preamplifier may be more suitable.
At Krohn-Hite, we offer a wide range of Electronic Test and Measurement Instruments, including DC Voltage and Current Source/Calibrators, Low-Noise Preamplifiers, Wideband Power Amplifiers, and Tunable and Fixed Frequenct Electronic Filters. Our products are designed to meet the diverse needs of industrial applications, providing high-quality solutions for signal amplification, signal conditioning, and noise reduction.
Whether you need a power amplifier to drive piezoelectric transducers or a preamplifier for signal conditioning, Krohn-Hite has you covered. Our team of experts is here to help you find the right amplifier for your application and provide support for all Krohn-Hite products. Contact us today to learn more about our product lines and how we can assist you with your industrial amplifier needs.
Is Bandpass Filter Better Than Low-Pass Filter?
When it comes to electronic filters, two common types are bandpass filters and low-pass filters. Both serve important functions in electronic circuits, but which one is better?
Understanding Bandpass Filters
Bandpass filters are designed to pass a specific range of frequencies while attenuating others. They consist of a combination of low-pass and high-pass filters that work together to allow only the desired band of frequencies to pass through. Bandpass filters are used in various applications, such as audio processing, telecommunications, and signal processing.
The main advantage of a bandpass filter is its ability to selectively pass a specific band of frequencies while blocking out unwanted frequencies. This can be beneficial in situations where you need to isolate a particular signal or remove unwanted noise from a circuit. Bandpass filters are also known for their sharp roll-off characteristics, which means they can effectively filter out frequencies outside of the desired range.
On the other hand, bandpass filters can be more complex to design and implement compared to low-pass filters. They typically require more components and precise tuning to achieve the desired frequency response. Additionally, bandpass filters may introduce phase shifts or distortions to the signal, which can be a consideration in certain applications.
Exploring Low-Pass Filters
On the other hand, low-pass filters are designed to pass frequencies below a certain cut-off frequency while attenuating higher frequencies. Low-pass filters are commonly used to remove high-frequency noise from a signal or limit a circuit's bandwidth. They are widely used in power supplies and data communications.
One of the main advantages of a low-pass filter is its simplicity and ease of implementation. Low-pass filters typically require fewer components and are easier to design compared to bandpass filters. They are also less prone to introducing phase shifts or distortions to the signal, making them suitable for applications where signal integrity is crucial.
However, low-pass filters have limitations in terms of frequency selectivity. They are not as effective at isolating a specific band of frequencies as bandpass filters. Low-pass filters also have a gradual roll-off characteristic, which may not be suitable for applications that require sharp frequency rejection.
Bandpass Filter vs. Low-Pass Filter: Which is Better?
So, which is better: a bandpass filter or a low-pass filter? The answer depends on your specific requirements and the nature of your application. If you need to isolate a specific band of frequencies while rejecting others, a bandpass filter would be the ideal choice. Bandpass filters are more effective at frequency selectivity and can provide sharper roll-off characteristics compared to low-pass filters.
On the other hand, if you need to remove high-frequency noise from a signal or limit the bandwidth of a circuit, a low-pass filter would be more suitable. Low-pass filters are simpler to design and implement and are less likely to introduce phase shifts or distortions to the signal.
Both bandpass filters and low-pass filters have their own strengths and weaknesses. The choice between the two will ultimately depend on your specific requirements and the goals of your electronic circuit. It is important to carefully evaluate your needs and consider the characteristics of each type of filter before making a decision.
Choose Krohn-Hite for Your Electronic Filter Needs
If you need high-quality electronic filters for your test and measurement applications, look no further than Krohn-Hite. Krohn-Hite is a leading manufacturer of Electronic Test and Measurement Instruments, specializing in DC Voltage and Current Source/Calibrators, Low-Noise Preamplifiers, Wideband Power Amplifiers, and Tunable and Fixed Frequenct Electronic Filters.
At Krohn-Hite, we are committed to providing our customers with reliable and accurate electronic instruments to meet their testing needs. Our product lines are designed to deliver superior performance and precision, ensuring you can always trust your measurements. Whether you need a bandpass filter, a low-pass filter, or any other electronic instrument, Krohn-Hite has you covered. Contact us today to discuss your specific requirements, and let us help you find the perfect solution for your test and measurement needs.
What Are the Advantages of a Low-Noise Preamplifier?
In the world of electronic devices and systems, noise is a persistent challenge that can significantly impact performance and reliability. Low-noice preamplifiers (LNAs) play a crucial role in minimizing unwanted noise and enhancing signal quality in a variety of applications.
What exactly is a low-noise preamplifier, and what are the advantages of using one? We will explore the benefits of low-noise preamplifiers and why they are essential components in many electronic systems.
Understanding Low-Noise Preamplifiers
Low-noise preamplifiers are electronic devices designed to amplify weak signals with the lowest possible added noise. They are commonly used in communication systems, radar systems, medical devices, and other applications where signal quality is critical.
The primary function of a low-noise preamplifier is to boost the strength of incoming signals without introducing additional noise that could degrade the signal-to-noise ratio. This is particularly important in applications where the signal of interest is weak or buried in background noise.
Advantages of a Low-Noise Preamplifier
1. Improved Signal-to-Noise Ratio
One of the primary advantages of using a low-noise preamplifier is its improved signal-to-noise ratio. By amplifying weak signals while adding minimal noise, LNAs help to enhance the clarity and reliability of the signal, making it easier to detect and analyze.
This improvement in signal-to-noise ratio is particularly beneficial in communication systems, where the quality of the signal directly impacts the accuracy and speed of data transmission.
2. Increased Sensitivity
Low-noise preamplifiers are essential for applications that require high sensitivity to weak signals. By minimizing added noise, LNAs enable electronic systems to detect and amplify low-level signals that would otherwise be lost in background noise.
This increased sensitivity is critical in fields such as astronomy, radio astronomy, and medical imaging, where the ability to detect faint signals is essential for scientific research and diagnostic purposes.
3. Greater Signal Integrity
In addition to improving signal-to-noise ratio and sensitivity, low-noise preamplifiers also help maintain the signal's integrity throughout the amplification process. LNAs ensure that the amplified signal remains faithful to the original input by minimizing distortion and interference.
This preservation of signal integrity is crucial in applications such as wireless communications, where signal quality directly impacts the clarity and reliability of voice and data transmissions.
4. Enhanced Performance
Overall, the advantages of using a low-noise preamplifier can be summed up in its enhanced performance in electronic systems. By improving signal quality, sensitivity, and integrity, LNAs contribute to the overall reliability and efficiency of the system, leading to better outcomes for users and operators.
Applications of Low-Noise Preamplifiers
Low-noise preamplifiers find wide-ranging applications in various industries and fields, including
- Wireless communications
- Satellite communications
- Radar and remote sensing
- Medical imaging
- Radio astronomy
- Test and measurement equipment
In each of these applications, the benefits of using a low-noise preamplifier are clear, with improved signal quality and performance leading to better outcomes for users and operators.
Choose Krohn-Hite for Your Low-Noise Preamplifier Needs
When it comes to high-quality, low-noise preamplifiers, Krohn-Hite is a trusted name in the industry. With a reputation for excellence and reliability, Krohn-Hite offers low-noise preamplifiers designed to meet the most demanding requirements of electronic systems.
Whether you need a low-noise preamplifier for communication systems, radar systems, or medical devices, Krohn-Hite has the right solution for your needs. Our products are known for their exceptional performance, durability, and precision, making them the ideal choice for critical applications where signal quality is paramount.
At Krohn-Hite, we are committed to providing our customers with the best possible solutions for their electronic test and measurement needs. Our product lines include DC voltage and current source/calibrators, preamplifiers, wideband power amplifiers, and tunable and fixed-frequency electronic filters, all designed to deliver reliable and accurate results in a variety of applications.
If you need a low-noise preamplifier or any other electronic test and measurement instrument, we encourage you to explore our website and learn more about our products and services. Whether you are a researcher, engineer, or technician, Krohn-Hite has the tools you need to succeed in your work.
10 Common Applications of DC Calibrators in Electronics
In the world of electronics, precision is key. Dependable tools are essential, from testing and measuring electronic devices to calibrating equipment for accurate readings. One such tool that plays a crucial role in ensuring accuracy is the DC calibrator. DC calibrators are used to generate stable and accurate DC voltage and current outputs for calibration purposes across a wide range of electronic applications.
1. Calibrating Multimeters: One of the primary applications of DC calibrators is calibrating multimeters. Multimeters are essential tools for measuring voltage, current, and resistance in electronic circuits. To ensure accurate readings, multimeters need to be calibrated regularly using a DC calibrator to verify their accuracy.
2. Testing Power Supplies: DC calibrators are also used to test and calibrate power supplies. Power supplies are crucial components in electronic devices that convert AC voltage to DC voltage for smooth operation. By using a DC calibrator, technicians can verify the output voltage and current of power supplies to ensure they meet specifications.
3. Calibrating Temperature Sensors: Temperature sensors are widely used in various industries to measure temperature accurately. To ensure the reliability of temperature readings, temperature sensors need to be calibrated regularly using a DC calibrator. This calibration process helps maintain the accuracy of temperature measurements.
4. Verifying Transducer Outputs: Transducers are devices that convert one form of energy into another, such as pressure into electrical signals. A DC calibrator is used to verify the output of transducers accurately and measure the response by applying a specific voltage or current signal to the transducer. This process helps ensure the transducer is functioning correctly.
5. Testing Control Systems: Control systems are used in industrial automation to monitor and control processes accurately. DC calibrators are essential tools for testing control systems by providing precise voltage and current signals to simulate various operating conditions. This testing helps ensure the reliability and accuracy of control systems in different applications.
6. Calibrating Electronic Meters: Electronic meters, such as wattmeters and energy meters, are used to measure electrical parameters in power systems. DC calibrators are used to calibrate electronic meters to ensure accurate measurements of voltage, current, power, and energy. Regular calibration using a DC calibrator helps maintain the accuracy of electronic meters.
7. Testing Circuit Breakers: Circuit breakers are safety devices that protect electrical circuits from overcurrents and short circuits. DC calibrators are used to test circuit breakers by providing controlled current signals to simulate fault conditions. This testing helps verify the proper operation of circuit breakers and ensures the safety of electrical systems.
8. Calibrating Data Acquisition Systems: Data acquisition systems are used to collect and record data from sensors and instruments for analysis. DC calibrators are essential for calibrating data acquisition systems by providing accurate voltage and current signals for sensor calibration. This calibration process helps ensure the reliability of data collected by the system.
9. Verifying Instrument Inputs: Various instruments, such as oscilloscopes and signal generators, have input channels that require calibration for accurate measurements. DC calibrators are used to verify the inputs of instruments by providing precise voltage and current signals. This verification process helps maintain the accuracy of instrument measurements.
10. Testing Electronic Components: Electronic components, such as resistors, capacitors, and diodes, need to be tested for their electrical characteristics. DC calibrators are used to test electronic components by applying specific voltage and current signals to measure their performance. This testing helps ensure the quality and functionality of electronic components.
5 Common Mistakes to Avoid When Using Electrical Test Equipment
Electrical test equipment is essential for ensuring the accuracy and reliability of electronic systems. Whether you are an experienced technician or a novice DIYer, using these tools correctly is crucial to prevent errors and ensure the safety of both yourself and your equipment.
Using the Wrong Test Equipment
One of the most common mistakes people make when using electrical test equipment is using the wrong tool for the job. Different testing tasks require different types of instruments, so choosing the right equipment for the task at hand is important. For example, using a multimeter to measure voltage when you actually need to measure current can lead to inaccurate readings and potential safety hazards.
Before starting any testing procedure, carefully consider the requirements of the task and select the appropriate test equipment. If you are unsure which tool to use, consult the user manual or seek advice from a qualified technician. Using the correct equipment will not only ensure accurate results but also prevent damage to your electronic devices.
Neglecting Calibration
Calibration is a critical aspect of using electrical test equipment properly. Regular calibration ensures that your instruments are providing accurate measurements and reliable results. Neglecting calibration can lead to inaccurate readings, which can result in faulty diagnoses and potentially dangerous situations.
To avoid this mistake, make sure to calibrate your test equipment regularly according to the manufacturer's recommendations. Some instruments may need to be calibrated annually, while others may require more frequent calibration. Keep track of the calibration schedule and make sure to adhere to it to maintain the accuracy of your measurements.
1. Improper Grounding
Proper grounding is essential when using electrical test equipment to prevent electrical shocks and ensure accurate readings. Improper grounding can lead to safety hazards and damage to your instruments, so following the manufacturer's guidelines for grounding procedures is crucial.
When using test equipment that requires grounding, make sure to connect the instrument to a properly grounded outlet or grounding rod. Avoid using makeshift grounding solutions or skipping this step altogether, as it can lead to serious consequences. If you are unsure about the grounding requirements of your equipment, consult the user manual or seek advice from a professional technician.
2. Failing to Inspect Equipment Before Use
Before using any electrical test equipment, inspecting the instrument for any signs of damage or wear is important. Failing to check the equipment before use can lead to inaccurate readings, malfunctions, and safety hazards. Look for signs of physical damage, such as cracks, frayed cables, or loose connections, and address any issues before proceeding with testing.
In addition to physical inspection, make sure to check the functionality of the instrument by performing a quick test to verify its accuracy. This can help identify any potential issues before starting a testing procedure, saving time and preventing errors. Regular inspection and maintenance of your test equipment will ensure its reliability and longevity.
3. Ignoring Safety Precautions
Safety should always be a top priority when using electrical test equipment. Ignoring safety precautions can lead to accidents, injuries, and damage to equipment. Always follow the manufacturer's safety guidelines and take necessary precautions to protect yourself and your surroundings.
When working with electrical test equipment, make sure to wear appropriate personal protective equipment, such as safety goggles and gloves, to prevent injuries. Avoid working alone, especially when testing high-voltage systems, and always disconnect power sources before making any adjustments or measurements. Taking proactive safety measures can prevent accidents and ensure a safe testing environment.
4. Not Understanding Equipment Specifications
Another common mistake people make when using electrical test equipment is not fully understanding the specifications of the instrument. Each piece of equipment has unique specifications, such as measurement range, accuracy, and operating conditions, which must be considered when performing tests. Failing to understand these specifications can lead to incorrect usage and inaccurate results.
Before using a new piece of test equipment, take the time to familiarize yourself with its specifications and capabilities. Consult the user manual or technical documentation to understand how to use the instrument and interpret the results properly. If you are unsure about any aspect of the equipment, do not hesitate to seek guidance from a knowledgeable technician or manufacturer.
5. Proper Storage and Handling
Proper storage and handling of electrical test equipment are essential for maintaining the accuracy and performance of the instruments. Improper storage can lead to damage, calibration drift, and premature failure of the equipment. To ensure the longevity of your test equipment, follow best practices for storage and handling.
Store your test equipment in a clean, dry environment away from dust, moisture, and extreme temperatures. Use protective cases or covers to prevent damage during transportation and storage. Handle the equipment with care, avoiding drops, impacts, and rough handling, which can cause physical damage and affect the accuracy of measurements. Properly storing and handling your test equipment can extend its lifespan and ensure reliable performance.
AC vs. DC Electrical Power Systems
AC vs. DC Electrical Power Systems In the realm of electrical power systems, two main types of currents dominate the landscape: Alternating Current (AC) and Direct Current (DC). Understanding the fundamental differences between these two forms of electrical power is vital for professionals in the field of electronics, electricians, and anyone working with electrical equipment.An Introduction to AC and DC Power Systems.
Before we delve into the differences between AC and DC power systems, let's first establish what each of these systems represents. Alternating Current (AC) is a type of electrical current in which the flow of electric charge periodically reverses direction. This reversal occurs at regular intervals, creating a waveform that oscillates between positive and negative values. AC power is commonly used in households and commercial buildings, as most electrical appliances and devices are designed to run on AC power.
On the other hand, Direct Current (DC) is a type of electrical current in which the flow of electric charge remains constant in one direction. DC power sources produce a steady flow of electrons from the negative terminal to the positive terminal, providing a consistent voltage level. While DC power is less common in household applications, it is widely used in electronic devices, batteries, and automotive systems.Understanding the Difference Between AC and DC
1. Voltage and Current Flow: One of the key differences between AC and DC power systems lies in how voltage and current flow through the system. The voltage and current periodically change direction in an AC system, creating a sinusoidal waveform. This fluctuation allows for efficient electricity transmission over long distances, making AC power ideal for powering homes, businesses, and industrial facilities. In contrast, DC systems maintain a constant voltage level, with the current flowing in one direction. This steady flow of electrons is suitable for powering electronics and devices that require a stable power supply.
2. Transmission and Distribution: AC power systems are well-suited for long-distance transmission and distribution of electricity. The ability of AC systems to easily step up and down voltage levels using transformers makes them ideal for transmitting power over vast distances with minimal energy loss. On the other hand, DC power is not as efficient for long-distance transmission due to higher energy losses. However, advancements in high-voltage DC transmission technology have made it more practical for certain applications, such as underwater cables and renewable energy projects.
3. Power Conversion: Another important distinction between AC and DC power systems is in power conversion. AC systems can easily be converted from one voltage level to another using transformers, which are essential for stepping up and stepping down voltage for different applications. DC power requires more complex conversion processes, such as rectification and inversion, to convert between different voltage levels. While DC systems are less versatile in terms of power conversion, they are more efficient for certain applications that require stability and precision.
4.
Safety and Reliability: When it comes to safety and reliability, both AC and DC power systems have their own advantages and drawbacks. AC power is considered safer for human contact due to its periodic reversal of direction, which reduces the risk of electrical shock. However, AC systems are more prone to voltage surges and harmonics, which can impact the reliability of electrical equipment. On the other hand, DC power is known for its stability and reliability, making it ideal for sensitive electronic devices. However, DC systems can pose a higher risk of electric shock if proper safety measures are not in place.Practical Applications of AC and DC Power Systems
Understanding the difference between AC and DC power systems is crucial for determining the most suitable power source for specific applications. Here are some practical examples of where AC and DC power systems are commonly used:
1. Household Appliances: Most household appliances, such as refrigerators, televisions, and air conditioners, run on AC power. The oscillating nature of AC allows these devices to operate efficiently and safely in residential settings.
2. Electronics and Computers: Electronic devices, such as computers, smartphones, and digital cameras, typically run on DC power. DC systems provide a stable voltage level that is essential for the proper functioning of sensitive electronic components.
3. Renewable Energy Systems: Both AC and DC power systems are used in renewable energy projects, such as solar and wind power. AC systems are commonly used for grid-tied solar installations, while DC systems are used for off-grid applications and battery storage systems.
4. Electric Vehicles: Electric vehicles (EVs) rely on DC power for charging and propulsion. DC fast chargers are commonly used to rapidly charge EV batteries, while onboard converters convert DC power from the battery to AC power for powering the vehicle's motor.
10 Best Practices for Using Electrical Test Equipment in Hazardous Environments
In today's industrial landscape, the task of testing electrical equipment is a critical component of ensuring the safety and reliability of machinery and processes. However, the stakes are even higher when working in hazardous environments such as oil refineries, chemical plants, or mining operations. The potential for explosions, fires, and other dangerous situations necessitates strict adherence to safety protocols when using electrical test equipment in these settings.
Understanding Hazardous Environments
Before diving into the best practices for using electrical test equipment in hazardous environments, it's essential to clearly understand what constitutes a hazardous environment. According to the National Fire Protection Association (NFPA), hazardous locations are classified based on the presence of flammable gases, vapors, liquids, combustible dust, or ignitable fibers. These environments are further categorized into different classes, divisions, and zones based on the nature and extent of the hazard.
When working in these environments, selecting electrical test equipment that is specifically designed and certified for use in hazardous locations is crucial. Equipment such as multimeters, oscilloscopes, and power supplies must meet stringent safety standards to prevent sparking, arcing, or other ignition sources that could lead to catastrophic events.
10 Best Practices for Electrical Safety Testing in Hazardous Environments
1. Conduct a Hazard Assessment: Before performing any electrical safety testing in a hazardous environment, it's essential to conduct a thorough hazard assessment to identify potential risks and determine the appropriate safety measures. Consider factors such as the presence of flammable substances, the likelihood of ignition sources, and the potential impact of a hazardous event.
2. Use Intrinsically Safe Equipment: When working in hazardous locations, it is crucial to use intrinsically safe electrical test equipment that is designed to prevent the release of sufficient energy to ignite flammable gases or vapors. For intrinsic safety, look for equipment that meets industry standards, such as ATEX, IECEx, or UL.
3. Follow Proper Lockout/Tagout Procedures: Before conducting any electrical testing, ensure all equipment is de-energized and locked out according to OSHA's lockout/tagout procedures. This will prevent accidental energization of circuits and minimize the risk of electrical shock or fire.
4. Inspect Equipment Before Use: Prior to using electrical test equipment in a hazardous environment, conduct a visual inspection to check for signs of damage, wear, or corrosion. Ensure all cables, connectors, and leads are in good condition and free of defects that could compromise safety.
5. Use Personal Protective Equipment (PPE): When working in hazardous environments, it is essential to wear appropriate PPE, such as flame-resistant clothing, safety glasses, gloves, and footwear. This will provide additional protection against potential hazards and minimize the risk of injury.
6. Minimize Exposure to Hazardous Elements: When conducting electrical safety testing in hazardous environments, take steps to minimize exposure to flammable gases, vapors, or combustible dust. Work in well-ventilated areas, use proper containment measures and avoid creating sparks or sources of ignition.
7. Implement Safety Barriers and Warning Signs: To prevent unauthorized access to hazardous areas, implement safety barriers and warning signs to alert personnel of potential risks. Restrict access to only authorized individuals who have received proper training in safety procedures.
8. Perform Regular Equipment Maintenance: To ensure the reliability and safety of electrical test equipment in hazardous environments, it is essential to perform regular maintenance and calibration checks. Follow manufacturer guidelines for inspection, testing, and servicing to keep equipment in optimal working condition.
9. Monitor Environmental Conditions: When working in hazardous environments, monitor environmental conditions such as temperature, humidity, and air quality to ensure they are within safe limits for electrical testing. Extreme conditions can affect equipment performance and pose additional risks to personnel.
10. Train Personnel on Safety Procedures: One of the most critical best practices for using electrical test equipment in hazardous environments is providing comprehensive training on safety procedures, emergency response protocols, and hazard recognition. Ensure that all staff members are familiar with proper safety precautions and know how to respond in case of an emergency.
Considering these best practices can help minimize risks and ensure the safety of personnel when conducting electrical safety testing in hazardous environments. By following strict safety protocols, using intrinsically safe equipment, and providing thorough training to personnel, you can create a safer work environment and prevent accidents or injuries.
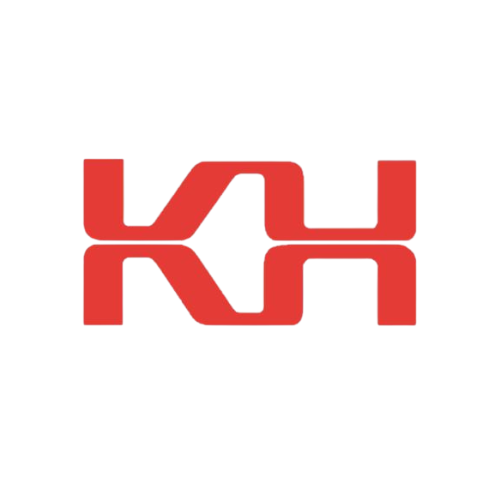